Provide you with the latest enterprise and industry news.
2.Insufficient Lubrication: Adequate lubrication is essential for reducing friction and minimizing wear between bearing surfaces. Insufficient lubrication or the use of incorrect lubricants can lead to increased friction, heat generation, and accelerated wear of bearing seats. Over time, this can result in surface damage, scoring, or seizure of bearings, leading to failure and downtime.
3.Contamination: Contaminants such as dirt, dust, moisture, or chemicals can infiltrate bearing seats, compromising their performance and longevity. Abrasive particles can cause abrasive wear, scoring, or scratching of bearing surfaces, while moisture and chemicals can lead to corrosion or chemical degradation of the seat material. Regular cleaning and sealing of bearing housings can help mitigate the risk of contamination-related failures.
4.Overloading: Excessive loads beyond the design capacity of bearing seats can cause deformation, plastic flow, or fracture of the seat material. This can occur due to overloading during operation or sudden impact loads caused by shock or vibration. Overloading can lead to fatigue failure, where repeated cyclic loading causes micro-cracks to propagate and eventually culminate in catastrophic failure of the bearing seat.
5.Vibration and Shock: Excessive vibration or shock loads can induce stress concentrations in bearing seats, leading to fatigue failure, fretting corrosion, or micro-cracking. Vibration can result from factors such as unbalanced rotating machinery, misalignment, or resonance frequencies in the system. Shock loads can occur due to sudden starts, stops, or impacts during operation, causing localized damage to bearing surfaces and compromising their integrity.
6.High Temperatures: Elevated temperatures in bearing applications can result from factors such as friction, overloading, or inadequate cooling. High temperatures can cause thermal expansion, softening, or degradation of the bearing seat material, reducing its mechanical properties and load-carrying capacity. Thermal cycling between hot and cold conditions can also induce thermal stresses, leading to thermal fatigue and eventual failure of the bearing seat.
7.Material Defects: Manufacturing defects in bearing seat materials, such as impurities, inclusions, or improper heat treatment, can compromise their structural integrity and mechanical properties. Common defects include voids, porosity, or inadequate grain structure, which can act as stress concentrators and initiate cracks or fractures under load. Material defects can lead to premature failure of bearing seats, necessitating replacement or repair.
8.Poor Maintenance: Neglecting regular maintenance practices, such as inspection, lubrication, and cleaning, can allow minor issues to escalate into major problems over time. Lack of lubrication or contaminated lubricants can accelerate wear and corrosion of bearing seats, while inadequate inspection can result in undetected defects or damage. Proper maintenance is essential for identifying and addressing potential issues early, prolonging the life of bearing seats and ensuring reliable performance.
9.Corrosion: Exposure to corrosive environments can lead to corrosion of bearing seat surfaces, compromising their structural integrity and mechanical properties. Corrosion can occur due to factors such as high humidity, saltwater exposure, or chemical contaminants in the environment. Corrosive attack can lead to pitting, rusting, or chemical degradation of bearing seat materials, reducing their load-carrying capacity and contributing to premature failure.
10.Fatigue: Fatigue failure in bearing seats occurs when repeated cyclic loading causes micro-cracks to initiate and propagate within the material, eventually leading to catastrophic failure. Fatigue can result from factors such as cyclic stresses induced by rotating machinery, fluctuating loads, or vibration. Over time, fatigue cracks can propagate through the material, weakening its structural integrity and leading to sudden failure of the bearing seat.
Bearing Seat
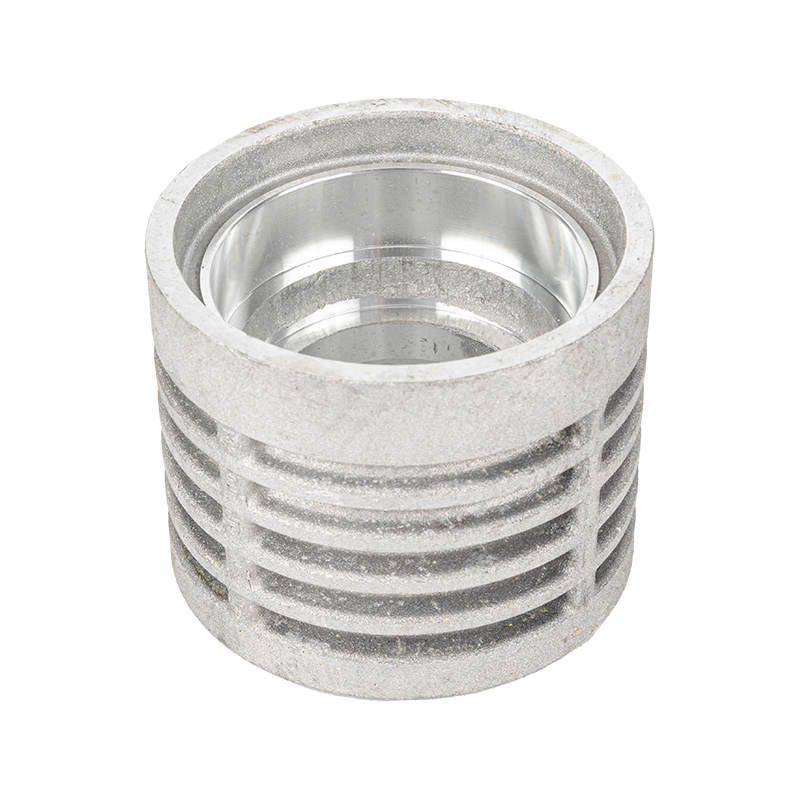